sixty61 series Collections
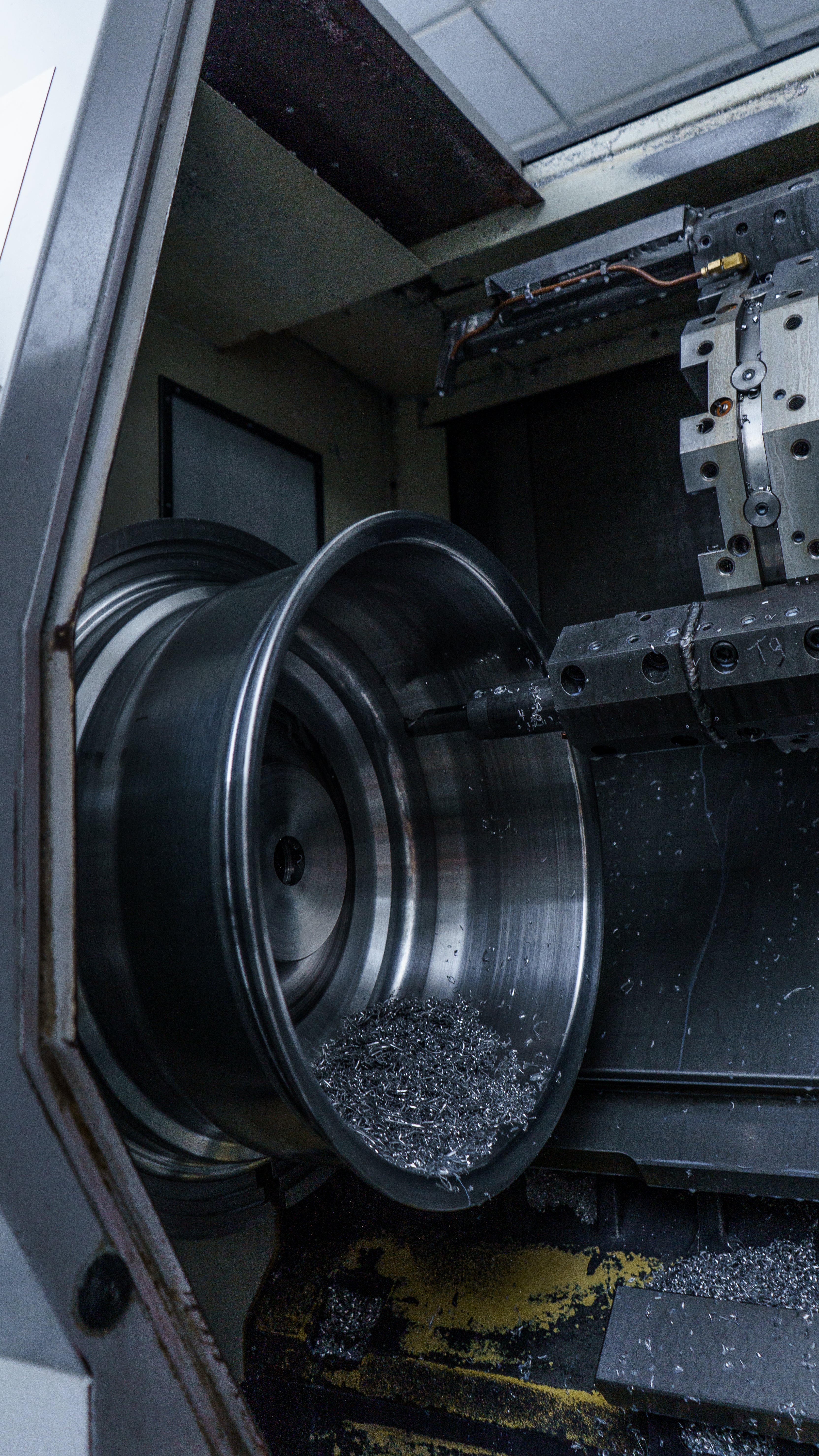
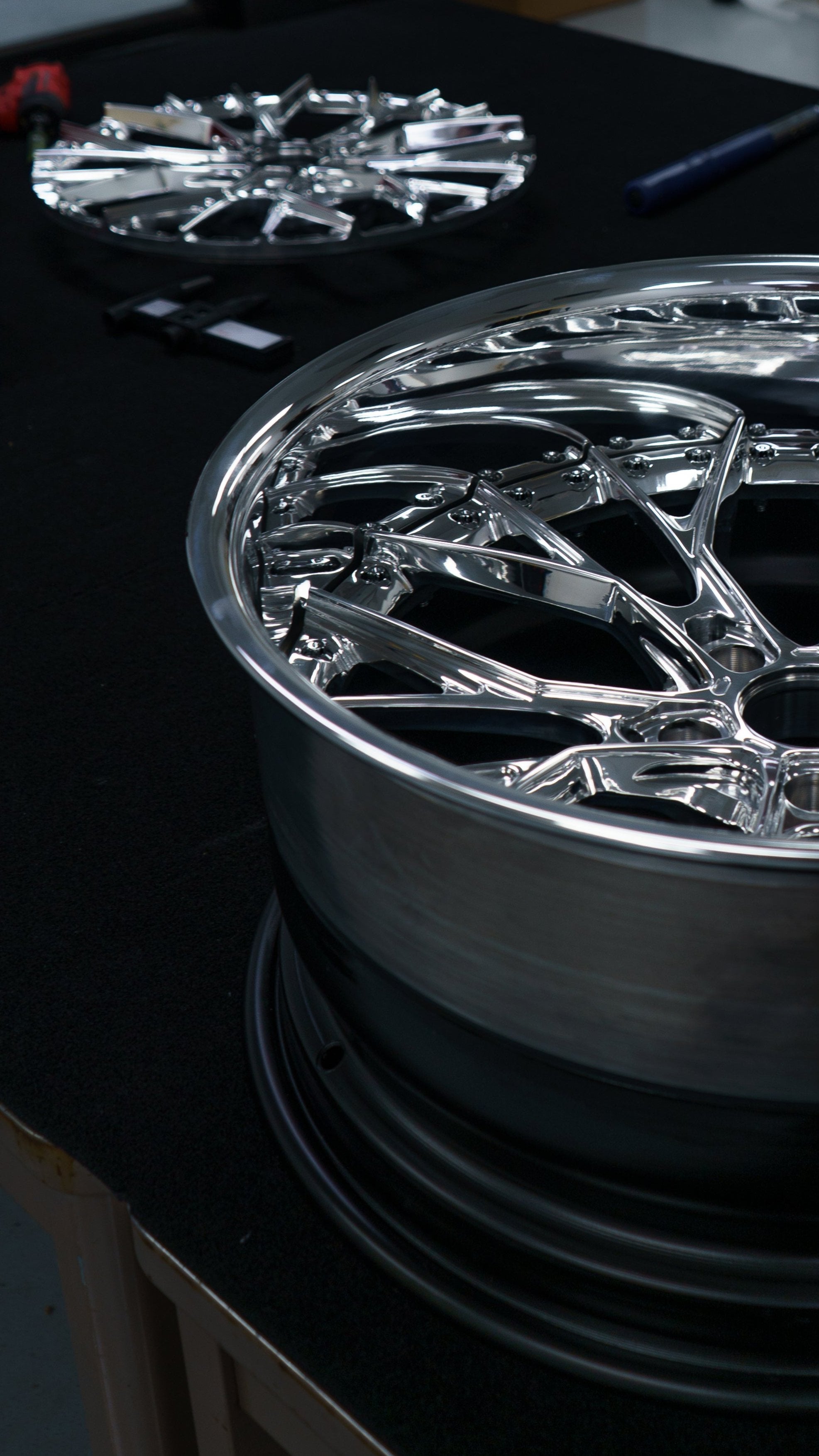
Introducing the sixty61 series
New for 2020, we’re proud to introduce the Sixty61 Series™, part of the Variant Wheels family. This series embodies innovation and versatility, offering forged wheel collections designed, engineered, and finished at our headquarters in Chandler, AZ. Each wheel is made from premium 6061-T6 aluminum, a material known for its strength, durability, and lightweight performance, making it perfect for high-performance applications. The Sixty61 Series is home to the Corsa Collection, Designer Collection, and Strada Collection. These forged wheel options allow us to build for virtually every bolt pattern, including center-lock vehicles, ensuring precise fitment across a wide range of vehicles. The multi-piece products offer unmatched flexibility, allowing us to achieve nearly any offset imaginable, making this collection the go-to choice for those seeking truly unique, custom wheels.
Whether for widebody builds, exotic supercars, or daily drivers, the Sixty61 Series is engineered to impress.
With the Sixty61 Series, you can choose from a variety of configurations:
• Monoblock (1P)
• Duo Block (2P)
• Three-Piece (3P)
• Three-Piece Floating Spoke (3P+)
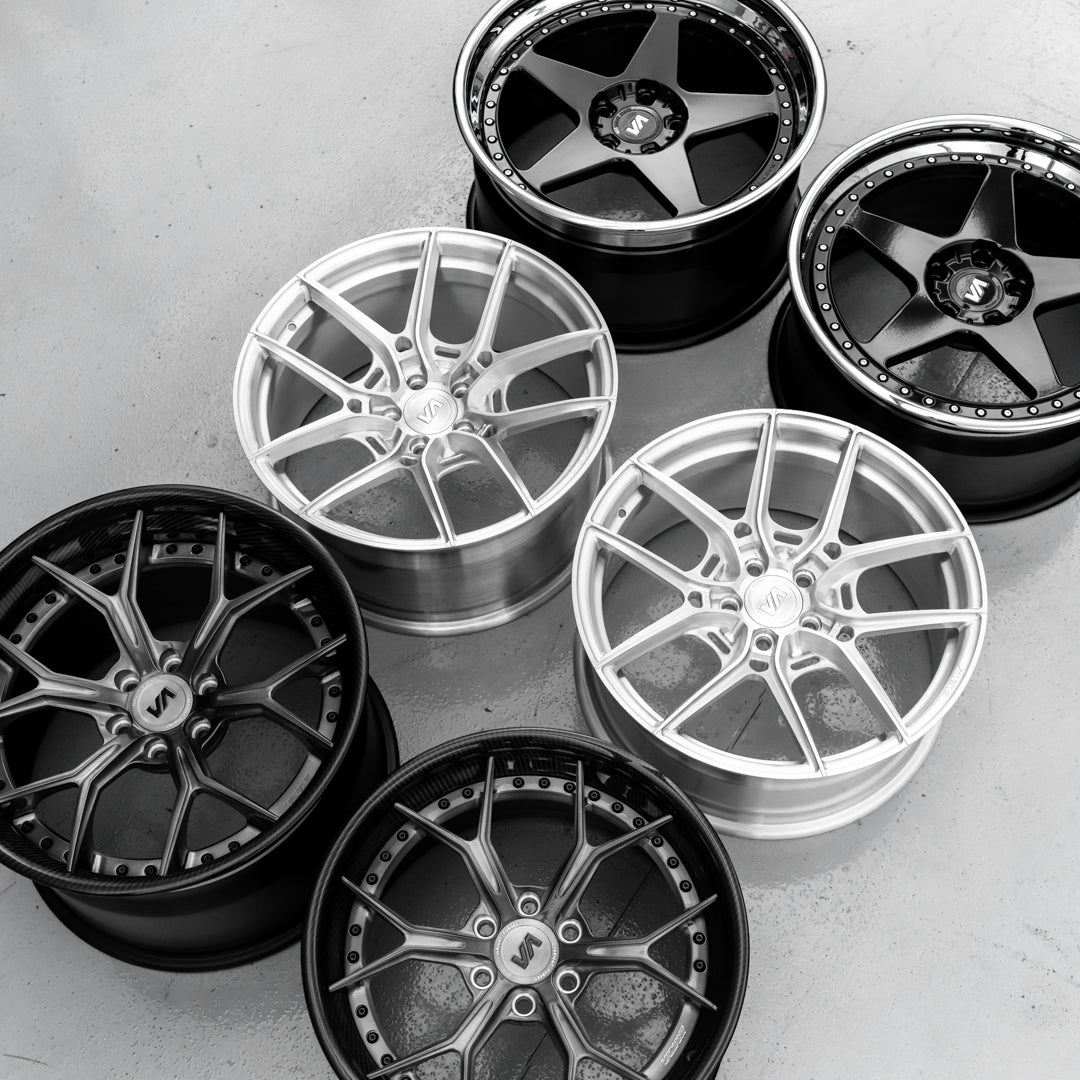
Ultimate Customization Options
Each wheel in the Sixty61 Series is designed from the ground up for every user, ensuring a completely personalized experience. With an average build time of 6–8 weeks, your custom wheels are meticulously crafted to meet your exact specifications.
From various concavity forgings to vast finish choices, every detail can be tailored to match your vision. Whether you prefer deep concave profiles for a bold, aggressive stance or a more subtle look, we offer a range of concave options to suit your style and performance needs.
You’ll also have access to an array of unique hardware finishes, lip styles, and multiple configurations, giving you endless possibilities to create wheels that are truly one-of-a-kind. With each wheel carefully crafted and custom-built, the Sixty61 Series provides you with a blank canvas to design your perfect set.
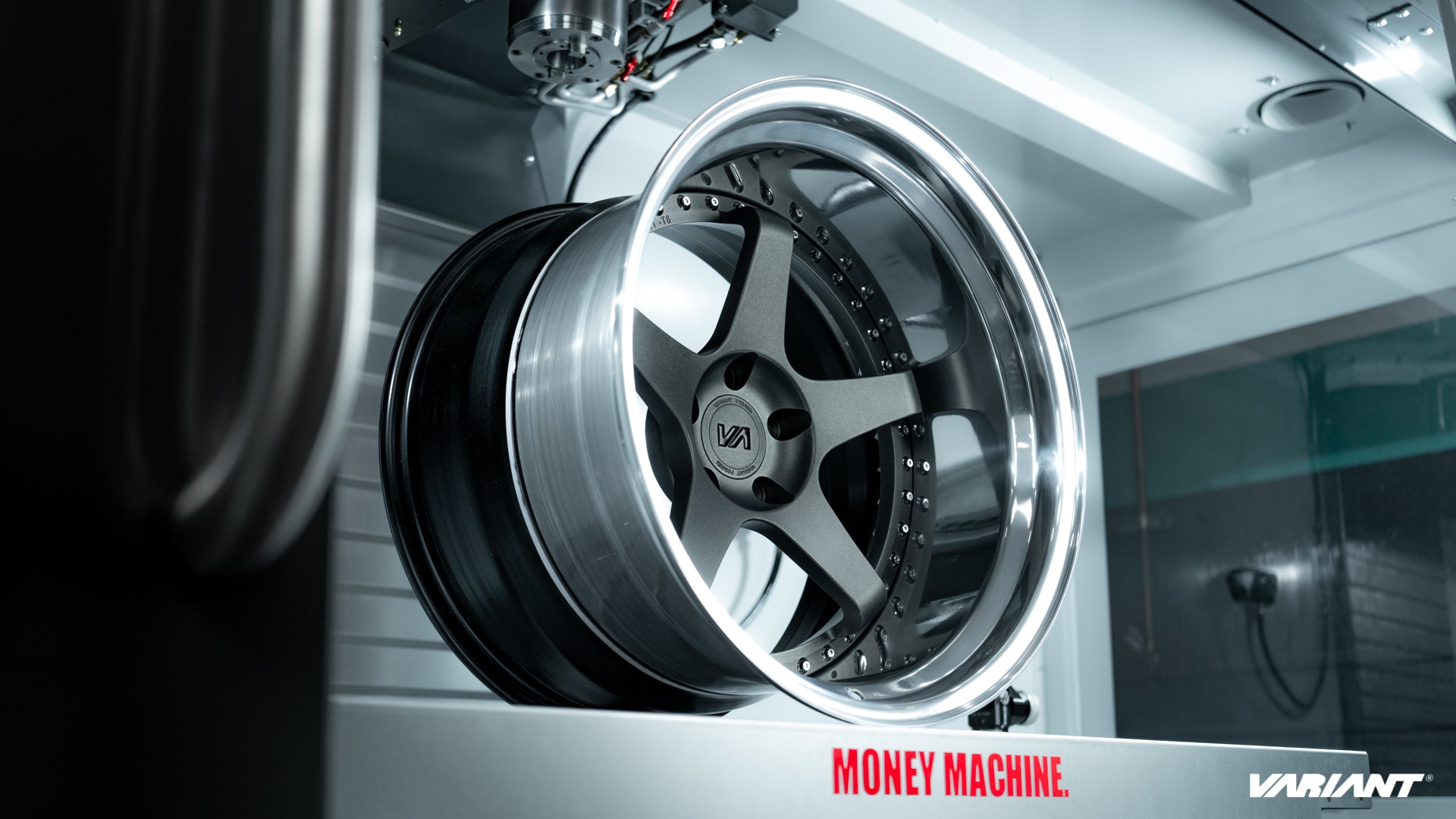
Built for the Future
As the Sixty61 Series continues to evolve, you can expect new styles and configurations to be added to our collections. Whether you’re a passionate car enthusiast or someone looking for that perfect blend of performance and aesthetics, the Sixty61 Series will help you achieve the look and feel you’ve always wanted.
Let us help you build your next set of custom forged wheels—crafted with precision, built for performance, and tailored to your unique style.
The Process
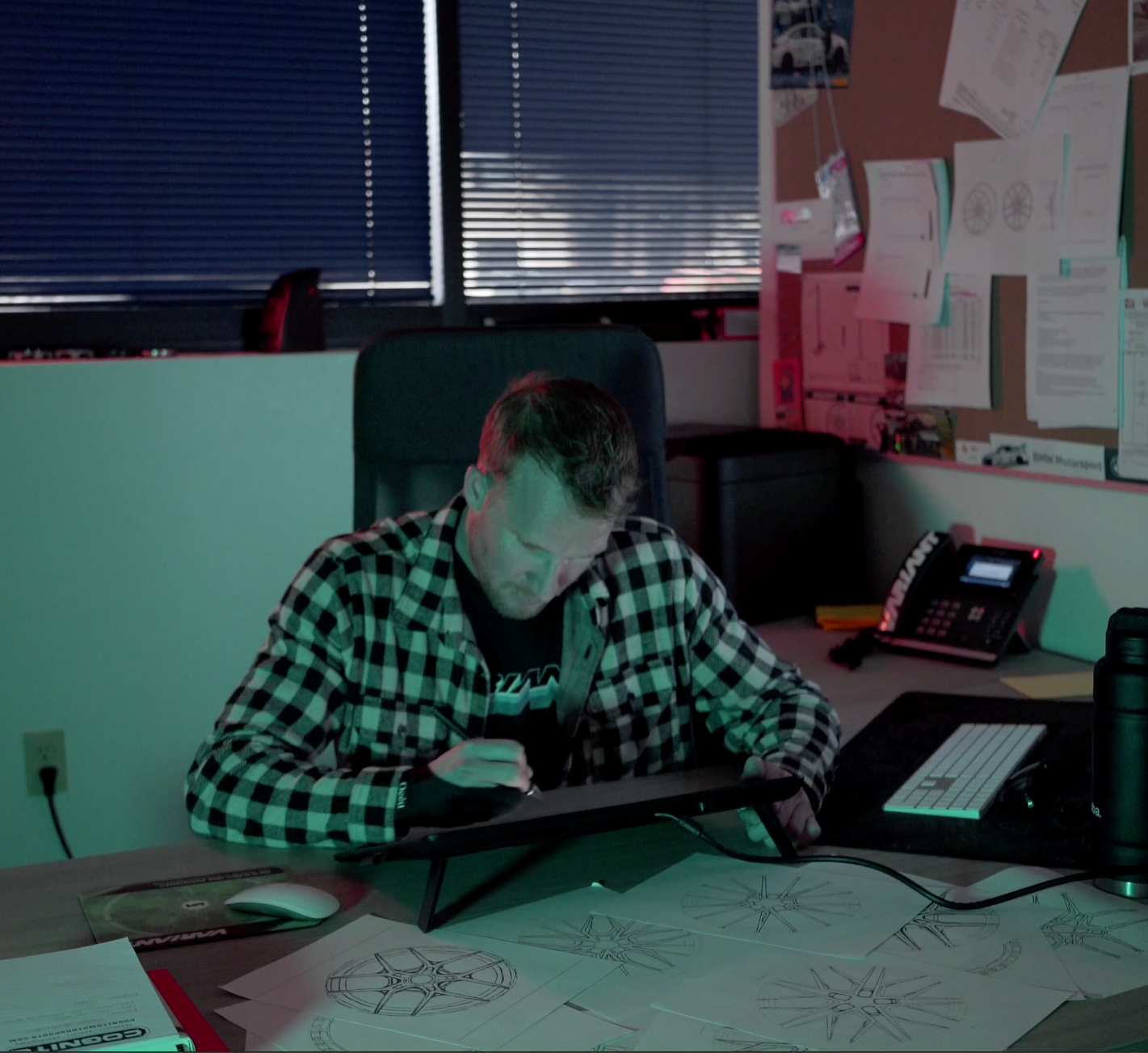
Design
It starts with a sketch...
Every custom wheel at Variant Wheels begins with the design team sketching initial concept ideas. By understanding the desired style and performance requirements, the team explores various shapes, profiles, and design elements that align with the vision. This phase allows creative possibilities to be brought to life, laying the foundation for a wheel that reflects individuality and performance goals. The concept sketches serve as the first step in transforming an idea into a fully realized, custom wheel design.
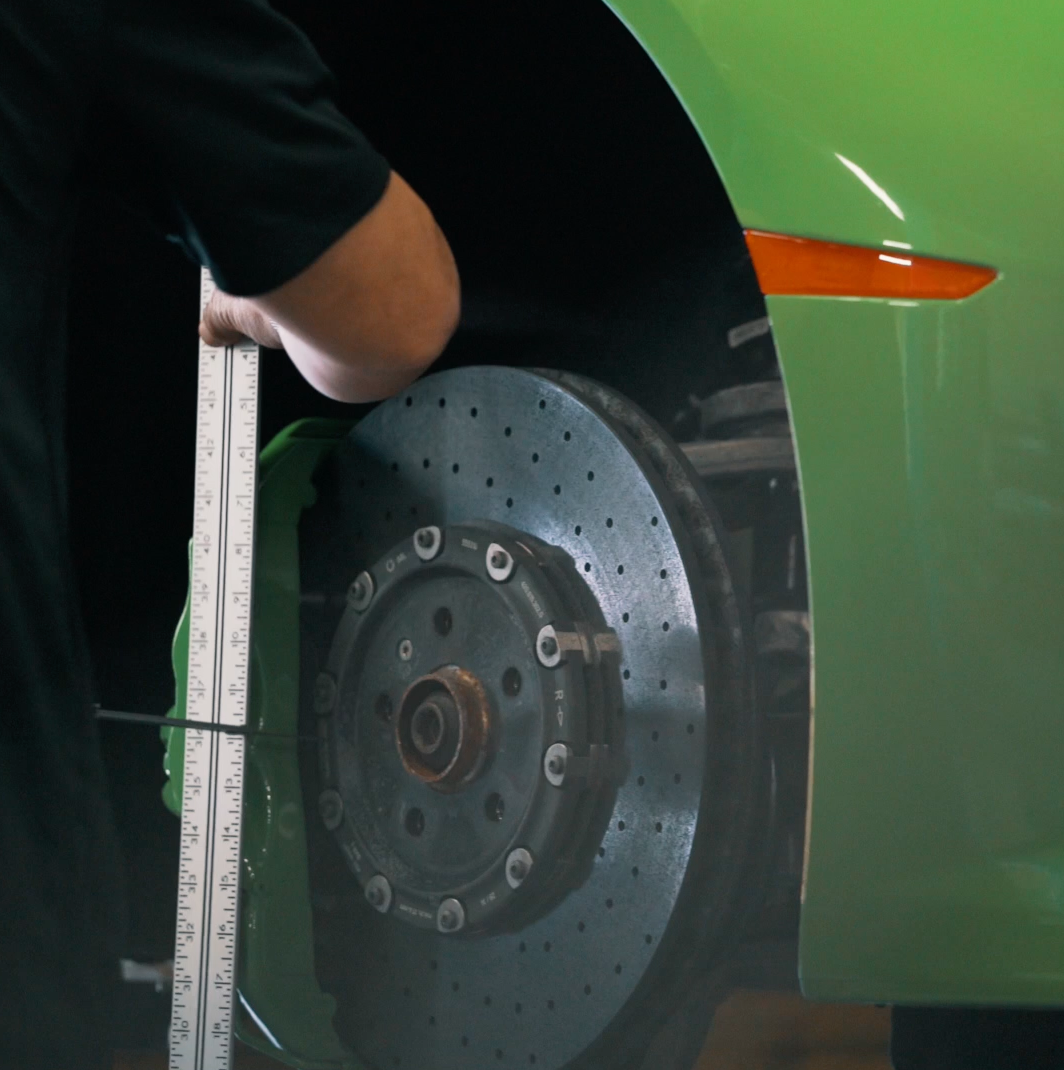
Fitment
Guaranteed Fitment
The next step is focused on fitment, where precision is key. At this stage, wheel sizes, offsets, brake clearances, and load ratings are carefully determined to ensure optimal performance and compatibility. Each design undergoes rigorous internal testing to guarantee that it meets the highest standards for both fit and safety. This meticulous process ensures that every wheel not only looks exceptional but also performs flawlessly, delivering the perfect combination of form and function.

Engineering
From Sketch to 3D Model
In the engineering phase, the concept sketch is transformed into a detailed 3D model. This is where the wheel truly begins to take shape. The engineering team programs both the lathe and mills, carefully selecting the tools needed to achieve the intricate features and precise details of the design. Every aspect is considered, from structural integrity to aesthetic details, ensuring the wheel meets exacting standards. This phase is crucial in bringing the design closer to production, with precision engineering guiding the way.
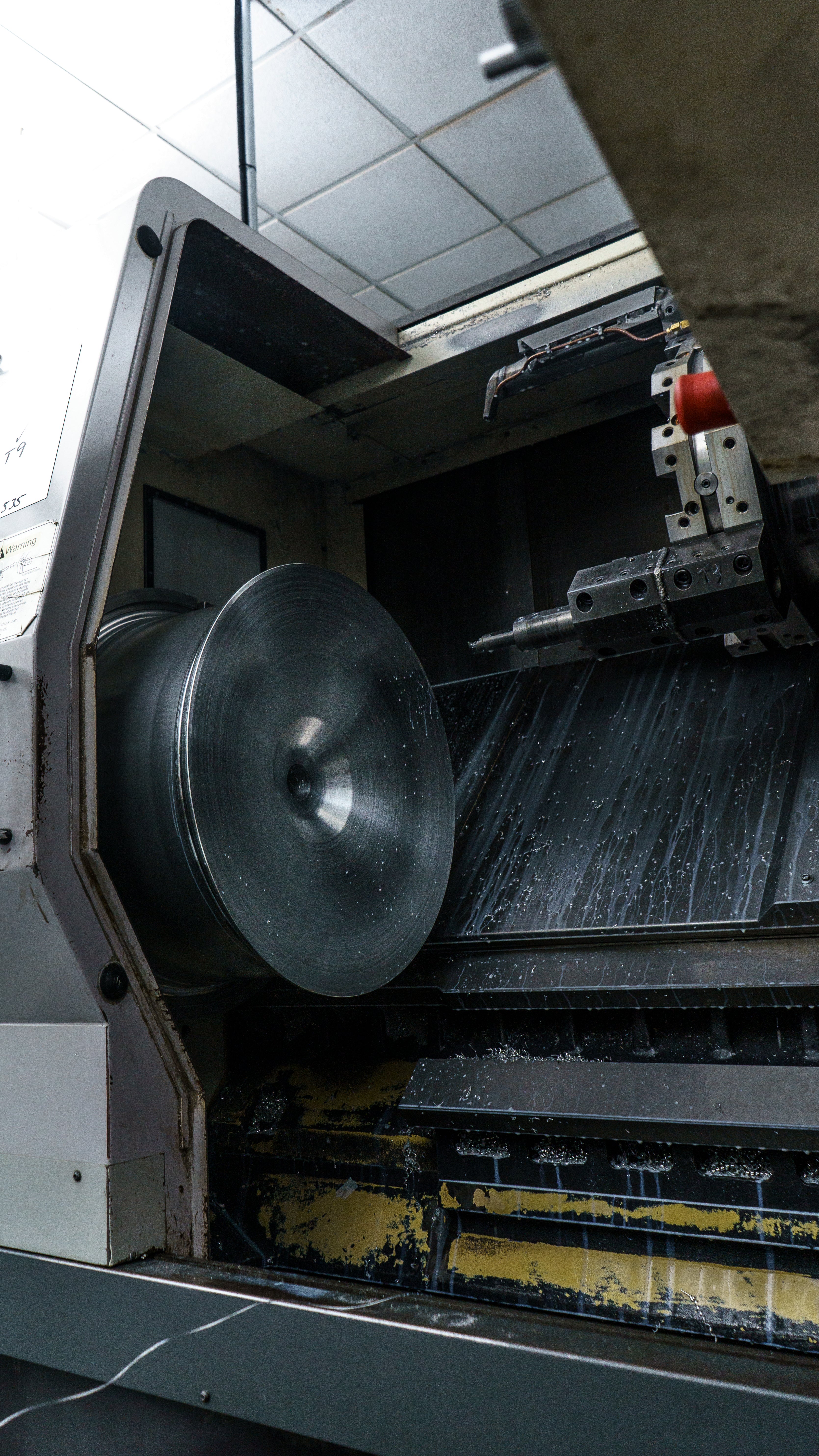
Lathe
Shaping the Raw Forgings
In the lathe stage, raw forgings are transformed using FEMCO S2000 lathes to shape the wheel and define its key features. This is where the concave profiles are turned and brake clearances are carefully machined to ensure optimal fitment and performance. Additionally, the center cap detail is added, and the preset center bore is precisely crafted. The lathe process establishes the core geometry of the wheel, laying the foundation for its final design and performance capabilities.
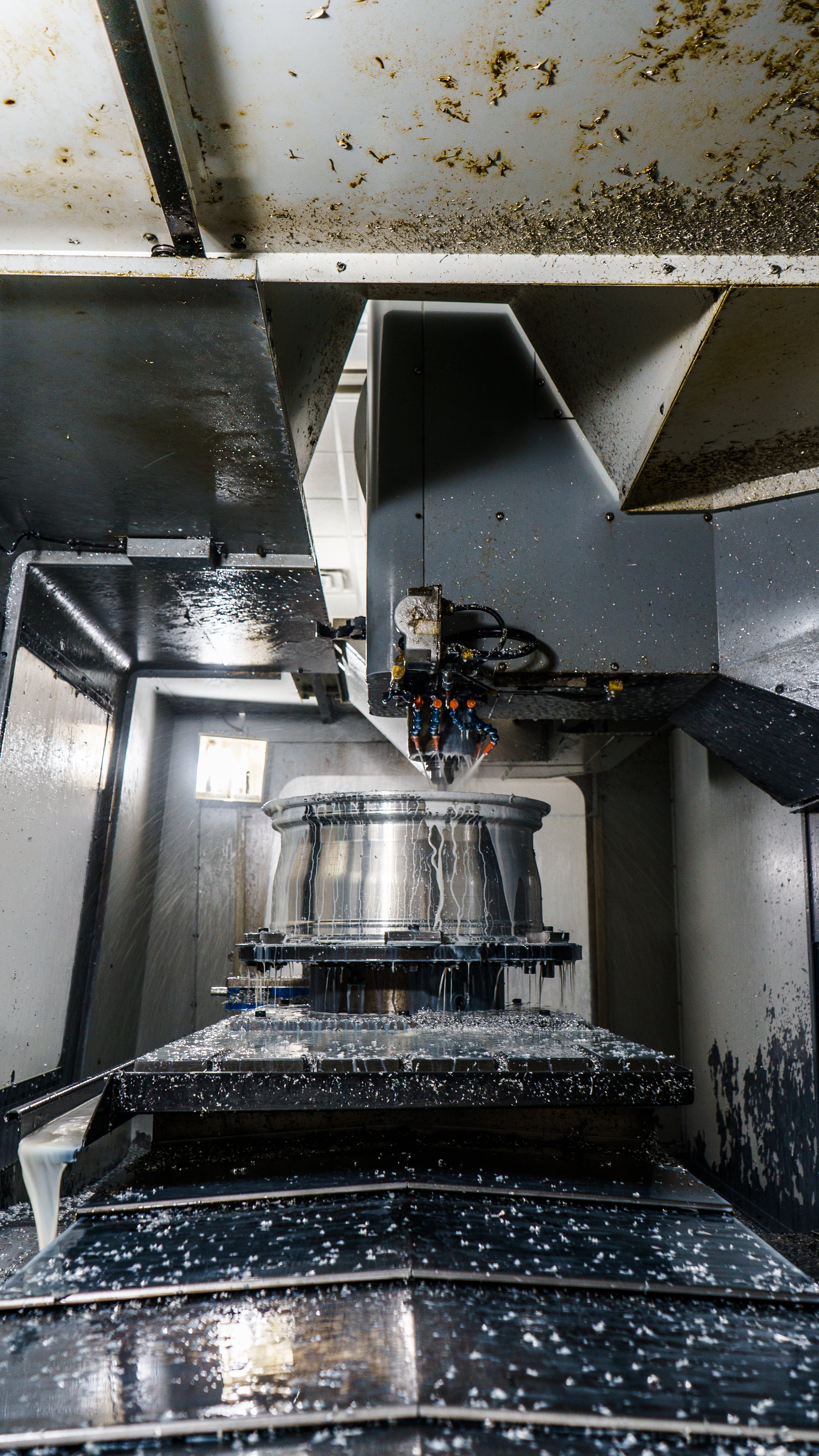
Mills
Under the knife.
The milling process is where the design is brought to life, as the wheel’s intricate details are cut from the existing material. At this stage, precision is key, with the goal of creating the lightest and strongest wheels possible—without ever sacrificing safety. Utilizing an extensive tool library, unique tool paths and cuts are made to achieve complex, eye-catching designs. This meticulous process ensures that every wheel not only looks stunning but also meets the highest standards for strength and durability.
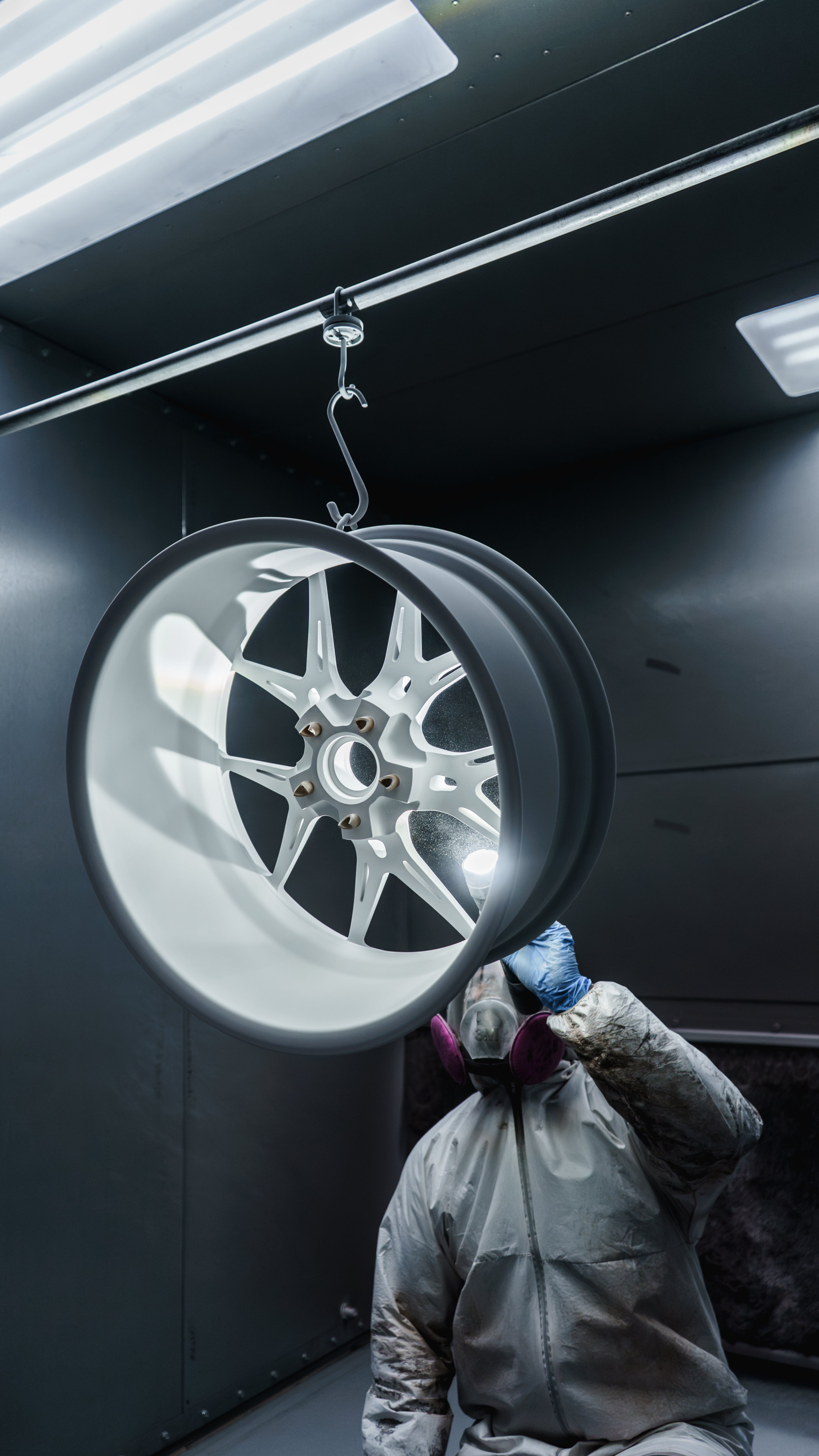
Finishing
Surface Perfection
The finishing stage focuses on refining and protecting the wheel. This begins with surface preparation, ensuring a flawless base for any additional finishes. Options like polishing or hand brushing are available to add a personal touch and elevate the wheel’s appearance. Each wheel is then coated with a powder coat top layer, which is baked at 400 degrees to create a durable and robust outer layer. This process not only enhances the look but also ensures long-lasting protection against the elements, giving each wheel a premium, high-quality finish.
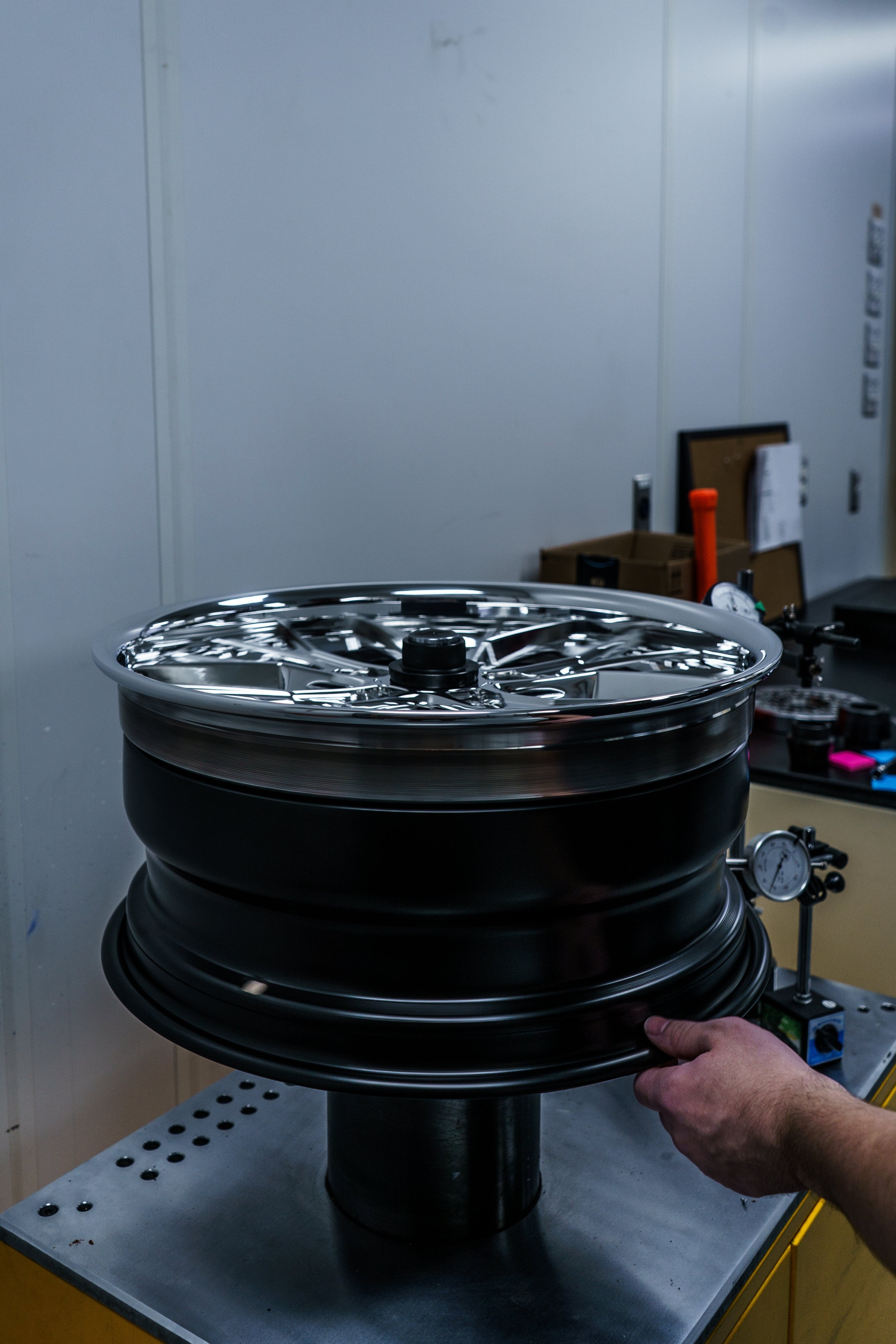
Assembly
Precision and Final Quality Checks
In the assembly phase, multi-piece wheels are carefully brought together, with each component meticulously assembled to ensure perfect alignment and functionality. This is also when center caps are added, completing the final look of the wheel. Before any product leaves the facility, rigorous final quality control checks are performed. Each wheel is inspected for blemishes in the finish, and runout tests—both lateral and radial—are conducted to ensure the highest standards of precision and performance. Only wheels that pass these thorough checks are approved for shipment, ensuring that every product leaving the facility is of the finest quality.
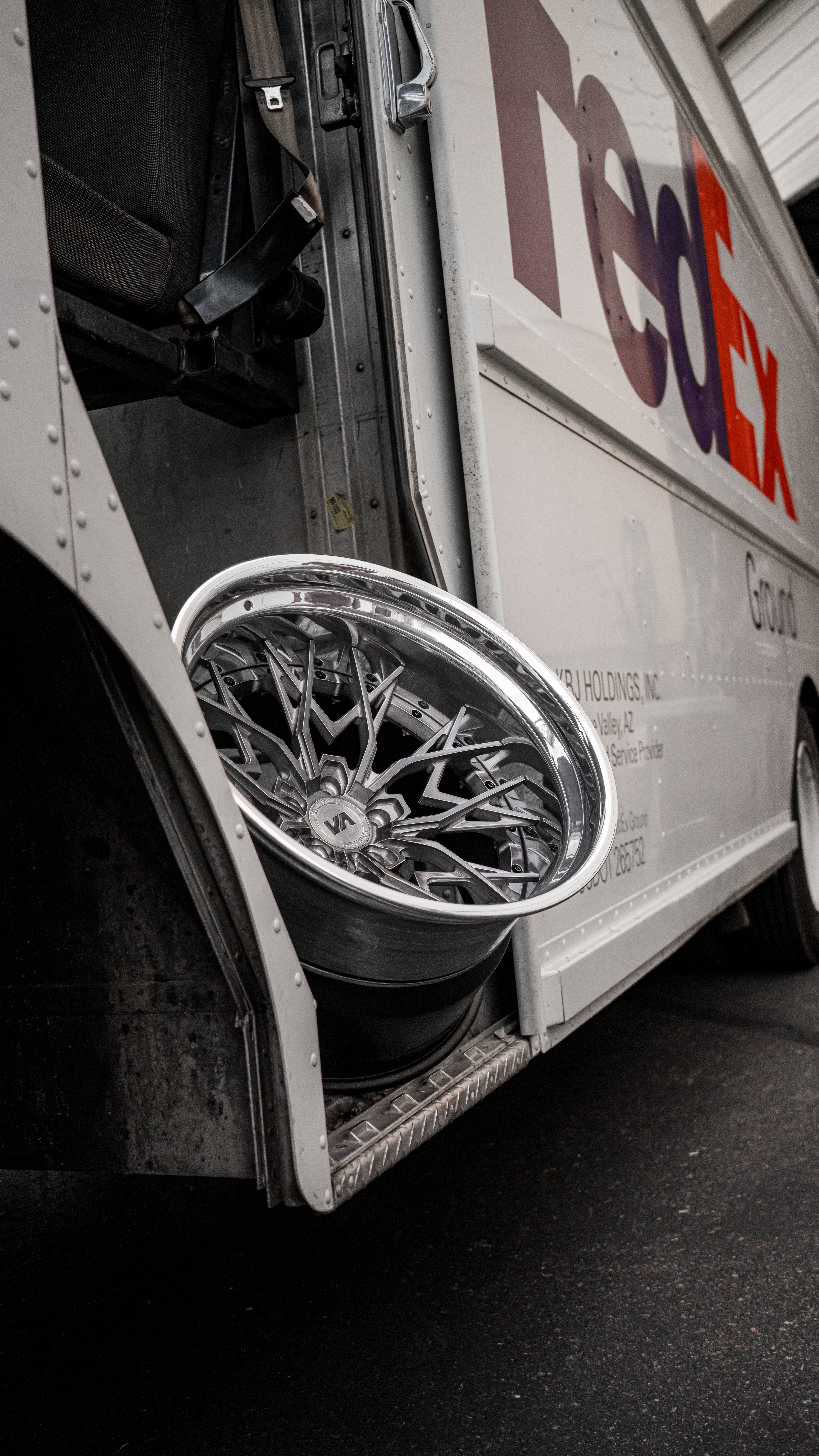
Shipping
Ready for the Road
Once a wheel has received its final approval, it enters the shipping stage. Each wheel is carefully packaged, ensuring it is fully protected for its journey. Any necessary accessory items are included, and shipping labels are generated for delivery to the final destination. The process is designed to ensure the wheels arrive in perfect condition, ready to be mounted and make their way onto the vehicles they were custom-built for. Every detail is handled with care, from the shop floor to the moment they are ready for installation.